Introduction:
While the efficiency of energy plays a crucial role in electric motor applications, some challenges, such as torque ripple, affect electric motor performance in a considerable way. Torque ripple is quite unexpected, but an intrinsic feature in electric motors with permanent magnets. While torque ripple is very difficult to prevent, it can be reduced to a suitable level, preserving the design parameters of the motor excellent. We have to select the right techniques to minimize the torque ripple to operate the motor perfectly.
To manage torque ripple for achieving high accuracy and control, MOSRAC motor provides appropriate solutions by its concentrated windings. With low cogging torque, MOSRAC motor can generate steady motion at low speed in different applications.
In this article, we will highlight some important design techniques for the reduction of torque ripple in electric motors, as well as the causes, effects and applications of torque ripple.
Understanding Torque Ripple in Electric Motors:
Theoretically, motors should provide steady and constant torque. However, frequent torque differences appear, causing torque ripple, due to the design and functional issues. Torque ripple relates to the irregular output of torque during the function of a motor.
There are three elements of torque ripple, such as cogging torque, reluctance torque and commutation torque. The relation between fixed magnets and stator slots creates the cogging torque, while magnetic reluctance in the rotor-stator combination causes the reluctance torque. Commutation torque is generated due to the switching operations. Mathematically, we can represent torque ripple as the change between the maximum and minimum torque generated through one cycle, divided by the average torque created by one cycle of the motor and defined by percentage.
Tripple = (Tmax – Tmin / Tavg) * 100
Figure 1: The contribution of cogging torque to torque ripple.
What are the Impacts of Torque Ripple?
1. Unstable Motion and Lower Accuracy:
Torque ripple can generate variations and irregularities in machine systems, degrading the features of the product.
2. Decreased Efficiency:
Torque ripple can increase the energy consumption, minimizing the efficiency of the motor.
3. Lower Lifespan:
Torque ripple produces vibrations and provides extra stress on motor elements, degrading their duration.
4. Generation of Vibration and Noise:
The stability of the motor operation can be degraded from the vibration and noise caused by torque ripple.
What are the Main Sources of Torque Ripple?
1. Generation of Cogging Torque:
In fixed magnet motors, the collaboration between the rotor magnets and stator teeth generates cogging torque. The variation of the torque output can be seen at low speed, operating the motor in a wrong way.
2. Saturation of Magnetic Materials:
The saturation phase of magnetic core elements plays a vital role in producing torque ripple in a magnetic field area in high power uses.
3. Commutation Issues:
The switching of current in motor windings causes torque ripple. This result is specifically marked at low speeds and the time between acceleration or deceleration.
4. Design Errors:
Torque ripple can be generated from distortions caused by the design errors shown in the stator or rotor.
5. Control Methods:
Enhanced control techniques have a major effect on torque ripple. To minimize torque ripple, modern control methods, like Field-Oriented Control (FOC), are quite efficient.
What is Field Oriented Control (FOC)?
Field Oriented Control (FOC) is an enhanced motor control method applied in electric AC motors. To operate the motor through the management of the torque and flux, the importance of FOC is quite high. To create the magnetic field in the stator, Magnetic Flux-Producing Current plays a crucial role. By regulating this current, FOC plays a critical role in increasing effectiveness, enhance magnetization, and minimize losses.
The aim of torque-producing current is to generate the motor’s torque. With varying loads, FOC can generate accurate and stable torque through regulating this current. In different functional conditions, FOC can enhance the effectiveness of the motor through the change in the flux. The reduction of torque ripple, caused by the decoupled technique between torque and flux, can produce a stable motor operation.
6. Presence of Slots:
Once the rotor rotates, the variations in the magnetic reluctance happen due to the existence of slots in the stator. This causes the changes in the magnetic field, generating torque ripple.
What are the Design Techniques to Reduce the Torque Ripple?
1. Design of Slots and Poles:
To minimize torque ripple in electric motors, choosing the slot and pole combination is an important issue. The number of slots and poles has a big influence on the harmonics of EMF and magnetic field, generating torque ripple. Due to the different alignment of magnets with the stator teeth, generating cogging torques in opposite directions and rejecting each other out, the fractional slot/pole number can minimize the cogging torque. Motors with a similar number of slots and poles include enhanced features, such as high efficiency, high power density, and low torque ripple.
What is Back EMF?
For the smooth operation and excellent performance of electric motors, the effect of Back electromotive force (back EMF) is quite significant. Within the coils, the revolution of the rotor can affect the magnetic force and movement. This effect generates a voltage in the coils, resisting the voltage in the motor's terminals. This resisting voltage is known as the back EMF.
The speed of the motor plays an important role in the back EMF. Quicker revolutions, higher numbers of turns in the rotor's windings and greater magnetic force produce a higher back EMF. The features of the rotor, including dimension, configuration and elements used, can affect the back EMF. The existence of back EMF is crucial for the functions of motors. Back EMF can control the current in the motor windings by resisting the applied voltage, providing protection from damage due to the excess current.
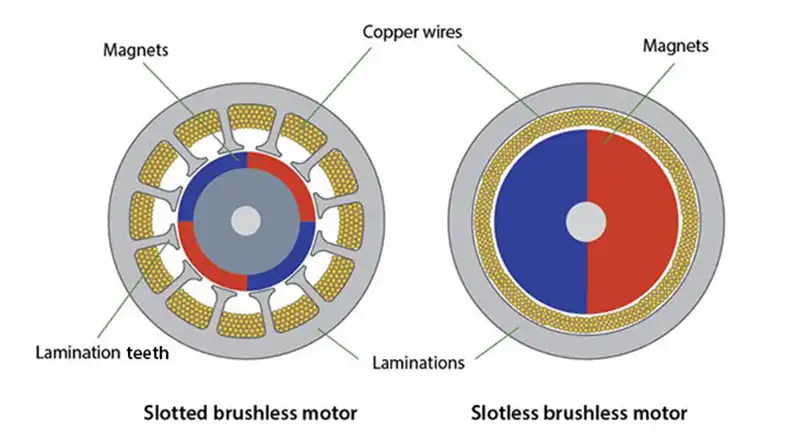
Figure 2: Slotless motors generate lower torque ripple than slotted motors.
2. Distributed Windings:
Distributed windings can prevent unexpected EMF harmonics, minimizing torque ripple. To produce the stable flux density in the air gap, distributed winding generates constant current and magnetic field around the rotor. With the reduction of fluctuations and torque ripple, this technique produces stable torque.
3. Separate Windings
By using the split-winding design, we can keep the torque steady for rotor locations. To reduce torque ripple, this design can minimize the changes of magnetic field.
4. Uneven Rotor Shape
To reduce torque ripple, an uneven rotor can change the flux density in the air gap to remove EMF harmonics.
5. Integration of Bias Magnetic Field
There are two types of magnetic fields in this design, such as secondary and primary. Torque ripples can be removed through the connection between these two fields. The modifications of rotor poles and stator slots are essential to generate a biased magnetic field to minimize torque ripple.
6. Magnet Skewing:
The inconsistent relation between the rotor and stator magnetic fields in a motor generates torque ripple. To minimize torque ripple, magnet skewing can angle the rotor magnets to maintain the stability of the magnetic force in the motor. By design and analysis, the skew angle should be selected to reduce torque ripple. There can be three kinds of magnet skewing, such as rotor skewing, stator skewing and segmented skewing.
7. Different Teeth Widths in Stator:
Using the similar teeth widths in the stator can produce different iron permeability that causes torque ripple. The application of the uneven teeth widths can reduce torque ripple. The width of each tooth is a crucial matter to achieve the similar flux density for all teeth.
8. Improved Control Techniques:
Control loops with high bandwidth and feedback with high resolution are quite efficient techniques to minimize torque ripple.
What are the Main Challenges of Torque Ripple?
1. Higher Difficulty:
Enhanced control methods and complicated designs require complex hardware and software that make the system sophisticated.
2. Greater Power Dissipation:
Motor efficiency can be reduced due to the higher power dissipation by using some techniques.
3. Higher Cost:
Cost can be high due to the application of advanced sensors and electronics that can cause problems for low-budget uses.
4. Maintenance Issues:
Due to the improved control systems, the requirements of the maintenance can be high, such as regular tests and calibrations.
5. Load Equivalency:
The operation of an oversized motor with a low load can generate torque ripple while an under-sized motor with high currents can cause torque ripple. We have to follow the load requirements for each motor.
Applications of Torque Ripple:
1. Automotive Industry:
Due to the high torque ripple effect in the stable operation of electric drivetrains, precise reduction techniques can be applied to enhance energy efficiency and reduce noise. Stable torque plays a crucial role in improved power steering systems.
2. Industrial Automation:
Torque ripple has a great effect on the accuracy and smooth motion of industrial automation. In the production area, stable torque can handle load management and reduces vibration for enhanced operations.
3. Aerospace:
Torque ripple reduction techniques provide stable and reliable operation of electronic actuation systems for control surfaces in aerospace applications. To minimize noise in electric propulsion systems and improve flight stability, smooth torque is quite essential.
4. Healthcare:
Accuracy in health care instruments, such as MRI scanners or surgical robots, relies on torque ripple-free motor functions.
Why Choose MOSRAC for Low-Cogging Torque Motor?
The special features of MOSRAC motors are high rigidity, high static load capacity, and accurate positioning that are essential for enhanced motion control applications. MOSRAC motors play a vital role in reducing cogging torque, which assists in extensive torque ripple minimization.
With its design and direct-drive configuration, MOSRAC torque motors can reduce torque ripple regarding conventional geared motors. The slotless design, combined with other features like concentrated windings, provides stable motion and low cogging torque. It removes the collaboration between stator teeth and rotor magnets that causes cogging. Due to its slotless stator design, the design of these motors reduce cogging torque.
Inrunner Frameless Torque Motor:
▪︎ Torque values: 0.025Nm to 50 Nm
▪︎ Voltage Ranges: 24 V to 48 V or custom-oriented.
▪︎ Outer Diameters: 25 mm to 200 mm or custom-oriented.
Figure 3: MOSRAC Inrunner Frameless Torque Motor
Outrunner Frameless Torque Motor:
▪︎ Torque values: 0.01Nm to 6Nm
▪︎ Voltage Ranges: 12, 16, 24, 36, and up to 48 V or custom-oriented.
▪︎ Outer Diameters: 14.9mm (0 587"), 22mm (0.866”), 49mm (1.929") up to 485mm (4.291") or custom-oriented.
Figure 4: MOSRAC Outrunner Frameless Torque Motor
Conclusion
Torque ripple is a fundamental property and challenge in electric motors that influence efficiency, stability, and direction. By understanding its causes, we can implement torque ripple reduction techniques for achieving smoother, more efficient motor operation in high-demand applications. This article provides extensive analysis to handle the challenges of torque ripple to enhance motor performance in various applications.
MOSRAC motors attain high precision with low cogging torque, which reduces ripple. With its low cogging torque, MOSRAC motor provides the customers other excellent benefits like integrated design, high torque density and effective operation that will be useful for different uses in industries. These motors apply to a slotless stator, removing the main reason for cogging torque. MOSRAC is prepared to assist the customers in selecting the right low-cogging torque motor for different applications.
If you have any questions or ideas related to Frameless Motors, Direct Drive Rotary Motors, and Encoders, contact us at sales12@mosrac.com for sales, technical inquiries, or order samples online today!
More FAQs About Torque Ripple
1. What is the Difference between Cogging Torque and Torque Ripple?
The attraction between the rotor and stator teeth at some rotor locations generates the cogging torque. On the other hand, the differences in the EMFs and their relations with the rotor and stator generates the torque ripple. All electric motors, including slotless motors, show torque ripple due to armature reaction.
Figure 5: Cogging Torque vs Torque Ripple
2. What is the relationship between sinusoidal commutation and torque ripple?
Sinusoidal commutation delivers sinusoidal currents to the motor windings, minimizing torque ripples in electric motors. While generating EMF, the main purpose of sinusoidal commutation is to produce steady torque and reduce the torque ripple. The integration between sinusoidal current and back EMF plays a vital role in establishing a consistent magnetic field.
3. What is the significance of predictive control techniques in removing torque ripple?
To lower the torque ripples in electric motors, predictive control techniques play a crucial task by controlling motor variables following the features of a motor. This insightful technique is quite significant for the minimization of torque variations generated by commutation and cogging. This method generates steady and accurate motor operations by uninterrupted predicting for torque variations.